Overview
In chemical production, achieving effective gas-to-liquid dispersion is essential for applications like gas absorption, chemical reactions, and mixing. Proper dispersion supports optimal reaction rates, increases gas-liquid contact area, and guarantees efficient blending of the components.
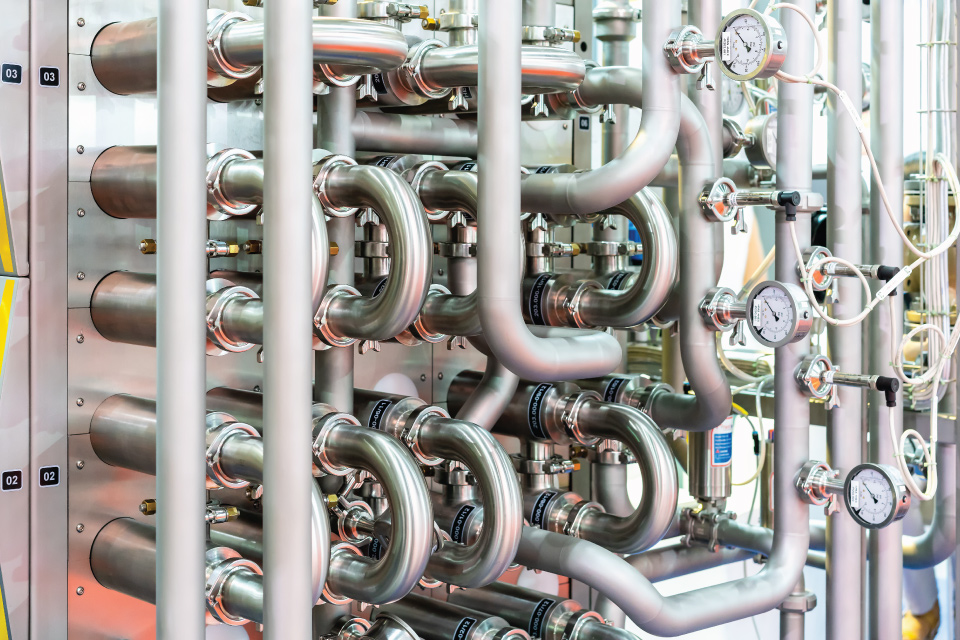
Direct Steam Injection heaters in gas-to-liquid dispersion provide precise temperature control and consistent mixing, enhancing process efficiency and product quality:
- Maintains consistent temperature for effective gas-to-liquid dispersion in chemical production, supporting optimal viscosity and gas solubility
- Achieves near 100% thermal efficiency with direct steam injection, maximizing energy transfer and minimizing waste in gas dispersion applications
- Reduces energy costs significantly in high-volume chemical processes, while supporting sustainability goals with efficient energy and water consumption
- Improves gas mixing and dispersion quality, enhancing surface contact and reaction rates for efficient gas absorption and catalytic reactions
- Reduces fouling and lower maintenance requirements by eliminating intermediary surfaces, ensuring reliable operation in continuous production environments
- Adapts easily to varying flow rates, temperatures, and gas concentrations, providing flexibility across multiple gas-to-liquid dispersion processes
- Saves valuable space in chemical plants with compact, easy-to-integrate design, streamlining installation and reducing structural modifications
- Enhances safety in processes involving hazardous gasses, thanks to immediate and precise temperature control that prevents unsafe conditions
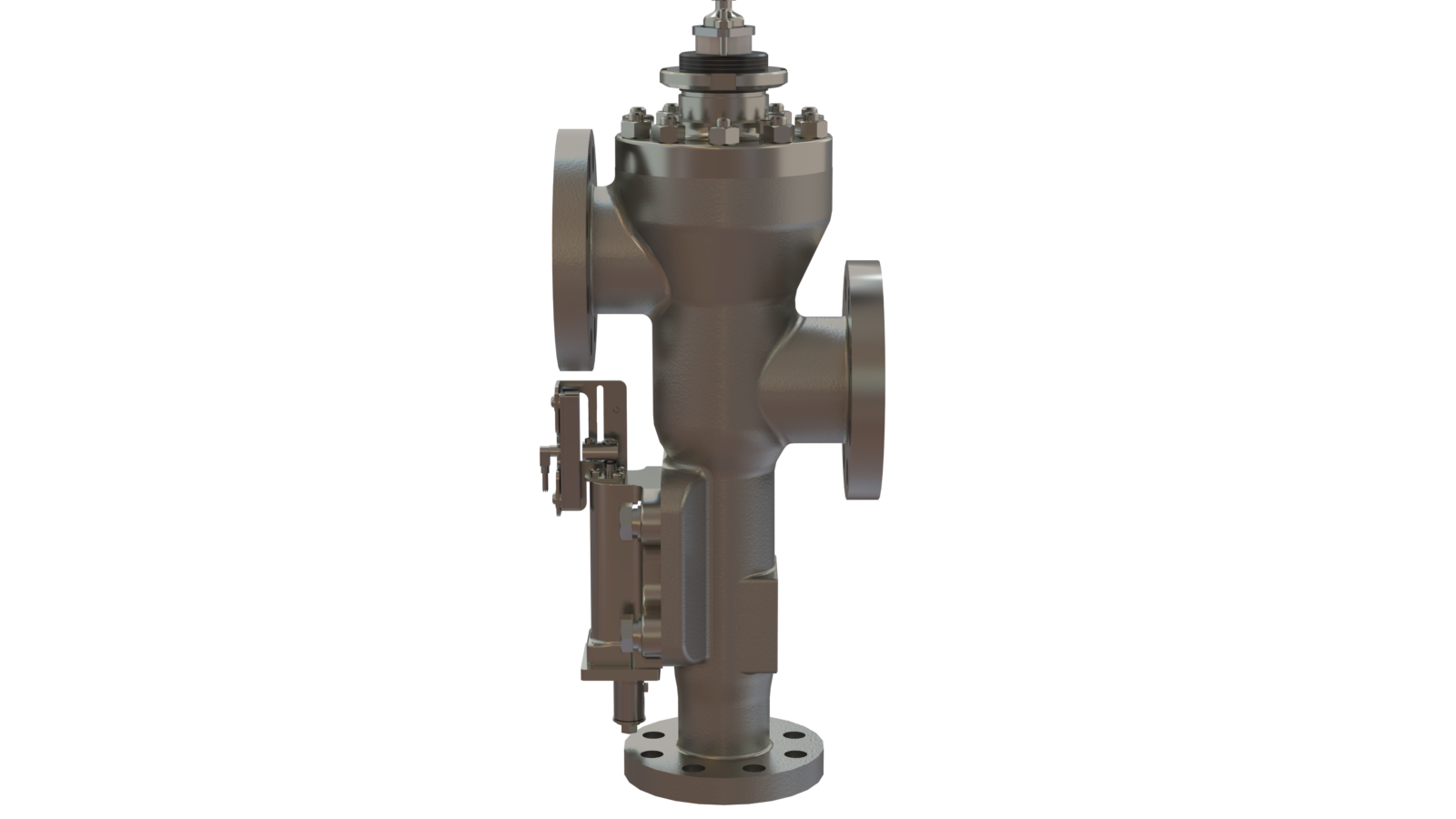
Hydroheater®
Also known as the Jetcooker™, our Hydroheater® has the longest proven history of heating and processing a complex range of liquids and materials. Known for its adjustability, durability, and power, the near century of engineering and innovation behind the design of this workhorse speaks for itself.
- Volume capability: 1 up to 6,700 gpm [0.2 up to 1,522 m³/hr]
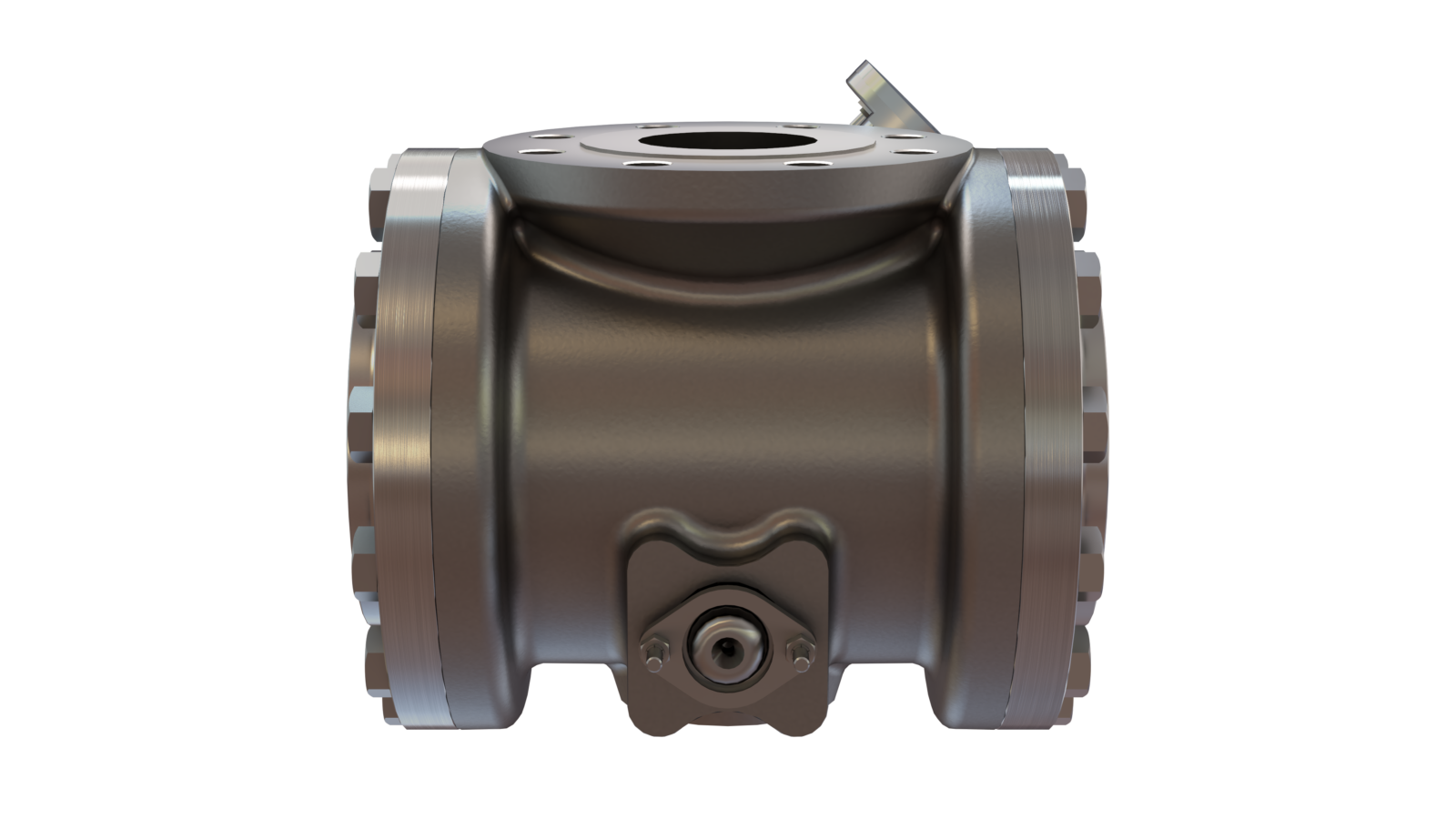
NOH™ (Non-Obstructing Heater)
The Non-Obstructing Heater is rugged enough to handle even the toughest abrasive materials, like sand and grit, to fibrous materials and large particulates.
- Its non-obstructive design protects against plugging, fouling, and pressure drop with its powerful, unrestricted flow.
- Volume capability: 30 up to 3,035 gpm [6.8 up to 689 m³/hr]
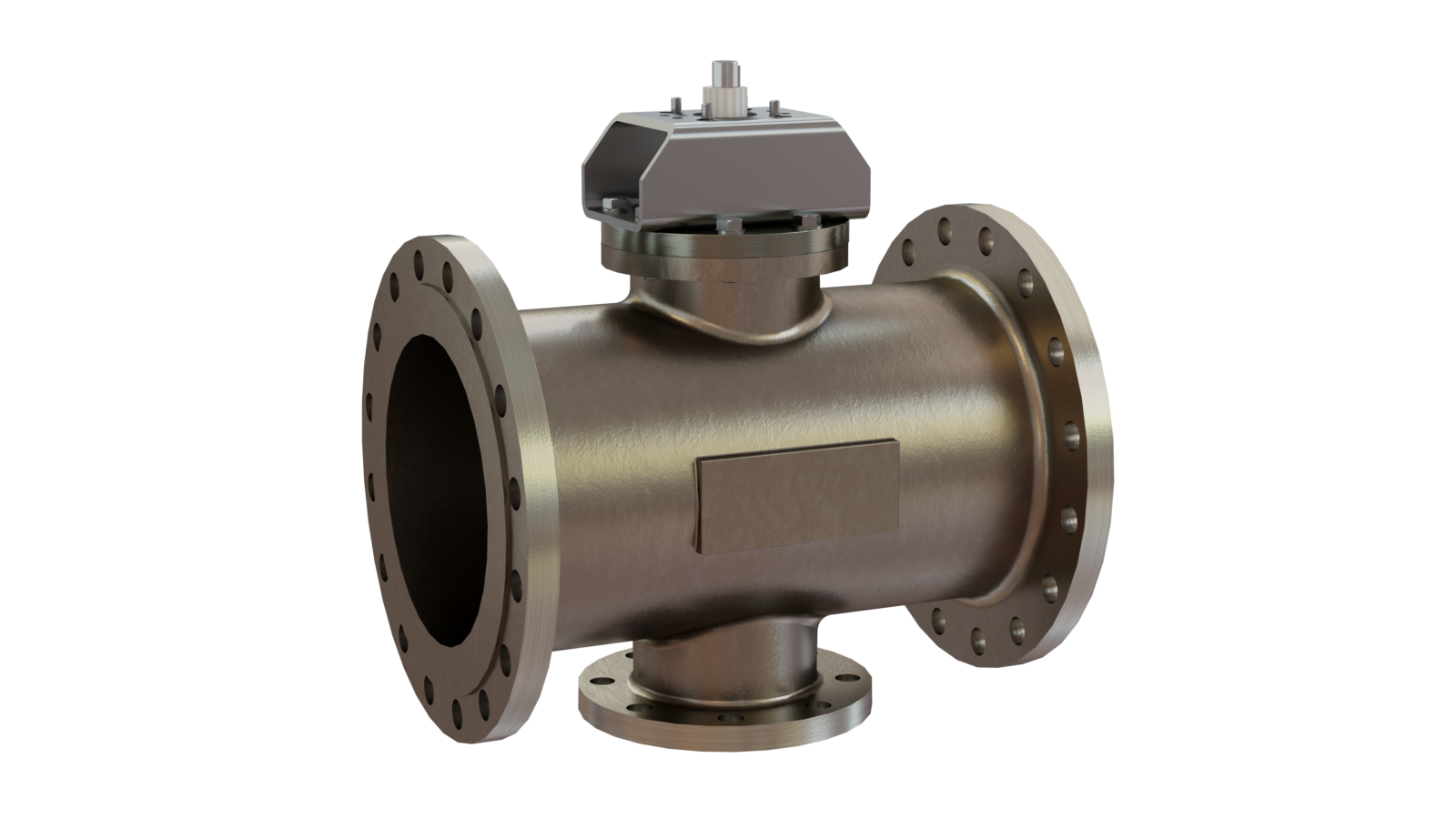
Solaris®
Perfect for viscous slurries, the Solaris® heater features an optimized straight-through design and low shear flow perfect for heavy slurries with medium consistency or higher solid contents. The flow diffuser injects steam across the entire cross-section to ensure thorough mixing and a uniform temperature profile even at a high volume and flow rate.
- Volume capability: 5 up to 25,000 gpm [1 up to 5,678 m³/hr]