Overview
Jacketed reactors are essential in various industries, including chemicals, pharmaceuticals, food production, and cosmetics, for processes that require controlled heating to ensure accurate reaction rates, product quality, and consistency. Traditional heating methods, such as indirect steam or hot water, can fail to deliver rapid, consistent heating.
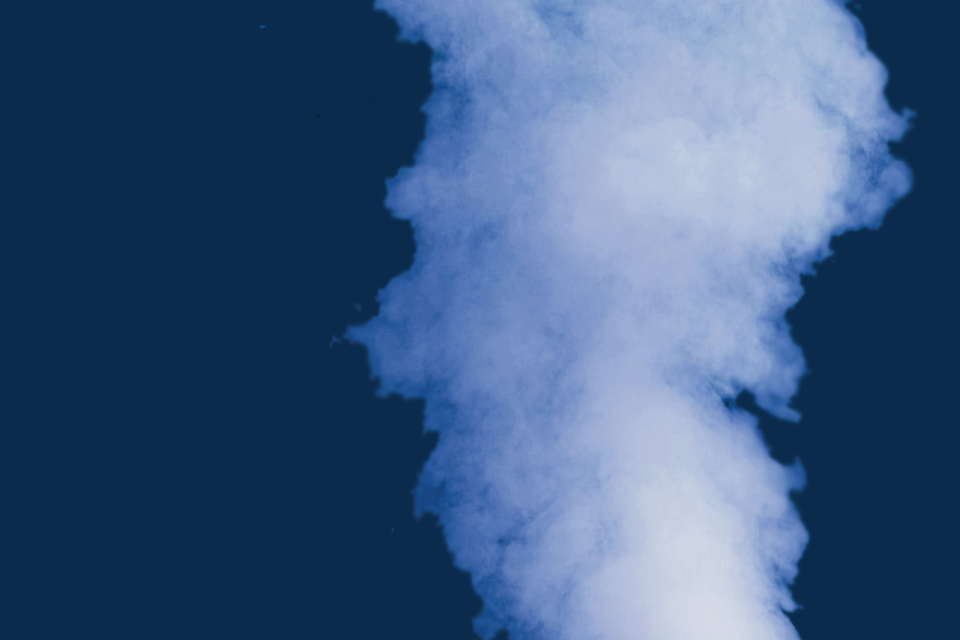
Direct Steam Injection (DSI) offers a fast, efficient, and precise solution that significantly enhances jacketed reactor operations:
- Provides fast, on-demand heating by directly injecting steam into the reactor jacket’s heat transfer medium, quickly reaching target temperatures to enhance production efficiency and throughput
- Offers precise temperature control for consistent process quality, enabling immediate adjustments to maintain exact temperatures, crucial for sensitive reactions and product integrity
- Ensures high energy efficiency with nearly 100% thermal transfer, reducing fuel consumption and operational costs, while supporting energy-saving and sustainability goals
- Reduces maintenance with minimal fouling risks, as direct steam injection avoids prolonged contact with heating surfaces, extending equipment life and reliability
- Delivers uniform heating across the reactor jacket, eliminating temperature inconsistencies that can lead to incomplete reactions or quality variations
- Enhances safety by minimizing steam leaks and reducing thermal shock to reactor components, improving equipment longevity and creating safer work conditions
- Adapts to varied production scales, offering scalable heating for batch or continuous processes, supporting flexible and expanding production demands